The spot welding machine connects two welding components (nickel sheet , battery cell, battery holder,and protective plate etc.) together through spot welding. The quality of spot welding directly affects the overall performance, yield, and battery life of the battery pack. Poor spot welding may also cause a risk of battery short circuit.
Here are some samples with defected welding result:

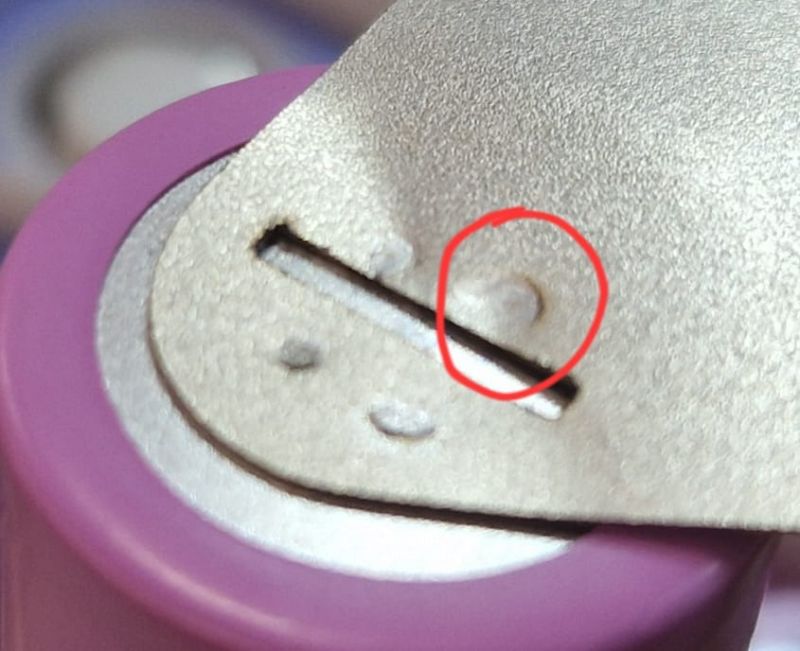
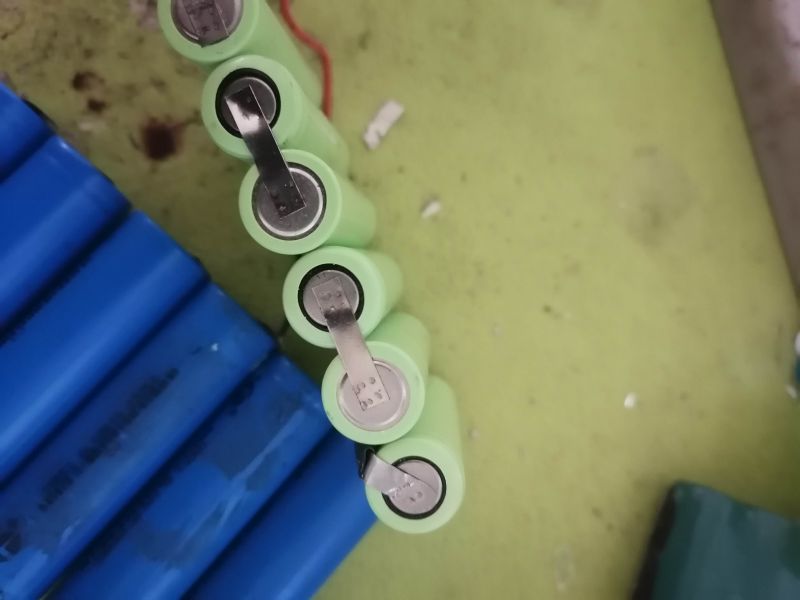
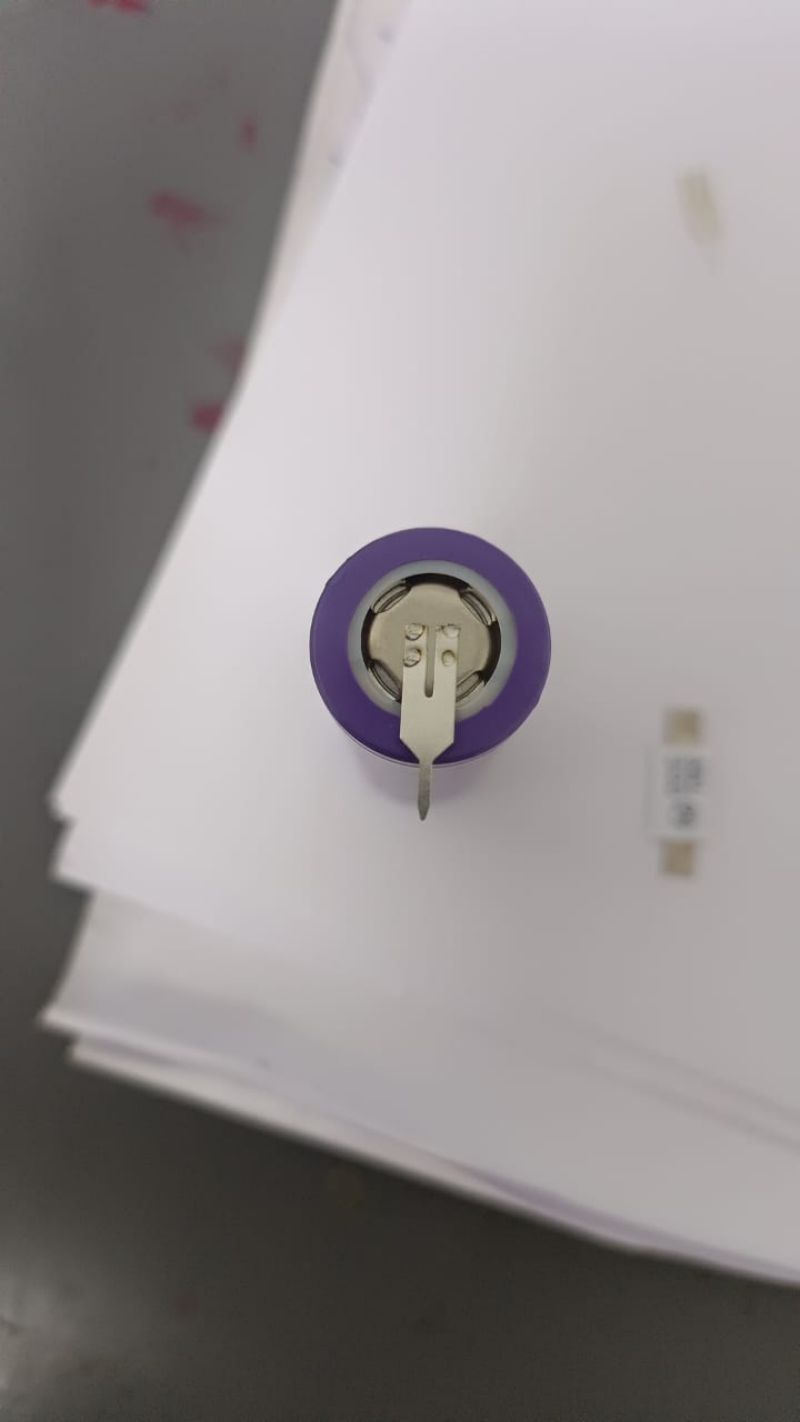
Battery spot welding machine is a high-efficiency and high-precision welding equipment, and the main process welding a battery is generally includes pre-welding preparation, welding process, and post welding treatment. In the preparation stage before welding, it is necessary to place the battery in the welding fixture, determines the welding position, and adjust the parameters. During the welding process, the battery spot welding machine melts the metal between the battery electrodes through high-temperature and high-pressure methods, forming a solid welding point. In the post welding stage, it is necessary to remove the welded battery from the fixture, and perform cleaning, testing, and other applicable treatment.
Further, some residues or pollutants may also be generated during the welding process. These residues may have certain impacts on the environment and human health. For instance, welding slag and metal oxides may be discharged into the environment with exhaust gas and wastewater, affecting water quality and atmospheric environment; Electrode powder may pose a hazard to the respiratory system and skin of operators. Therefore, it is important to choose a suitable spot-welding equipment for precise welding of battery packs.
That said, by using Styler's transistor precision spot welding equipment, the welding process can be completed in a short period of time, with minimal welding heat impact, and no splashing during the welding process. It is not only suitable for precision welding, but also for small, high-performance electronic components, and the assembly of small components in the precision machinery industry. For example, thin wires, button batteries, small contacts of relays, and metal foil.
Styler's precision welding equipment has five control modes: constant current, constant voltage, constant current & constant voltage combination, constant power, and constant current & constant power combination modes, which is switchable manually; 32 sets of energy options are switchable through external ports; The input & output signal features are available that compatible with the full-automatic production line; Built-in detection function: Before formal power on, there can be a detection current to confirm the presence and status of the workpiece.
The following is a display of the battery pack welded using the Styler's PDC10000A transistor precision welding equipment:
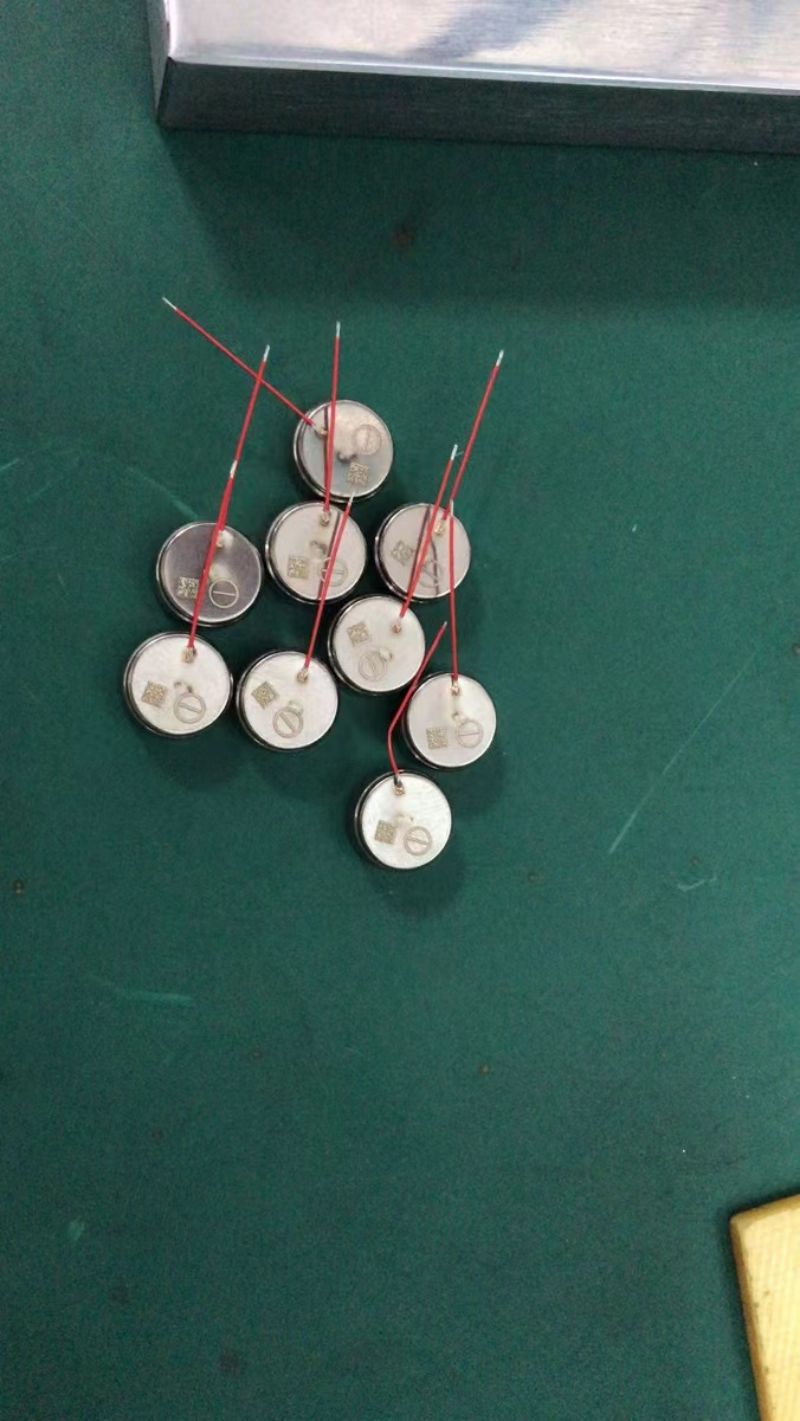
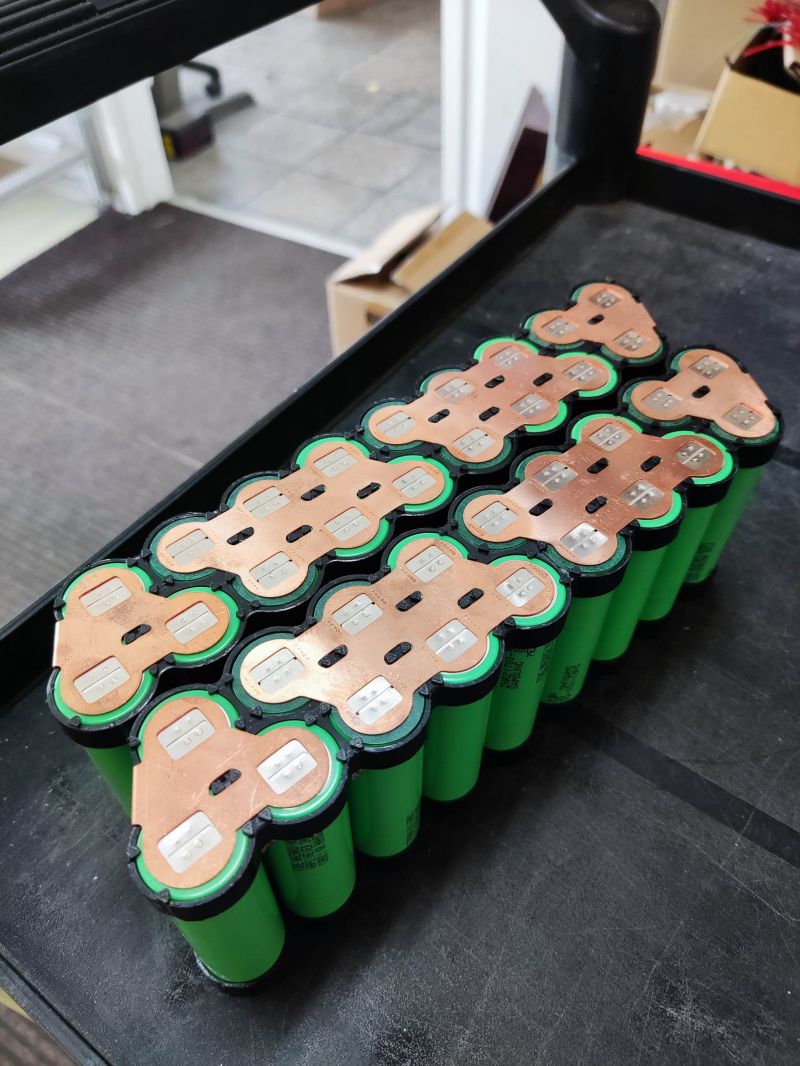

If you are looking for a welding machine that suitable for your business, please contact us today, or check out the product page PDC10000A transistor precision welding equipment
The information provided by Styler (“we,” “us” or “our”) on (the “Site”) is for general informational purposes only. All information on the Site is provided in good faith, however, we make no representation or warranty of any kind, express or implied, regarding the accuracy, adequacy, validity, reliability, availability or completeness of any information on the Site. UNDER NO CIRCUMSTANCE SHALL WE HAVE ANY LIABILITY TO YOU FOR ANY LOSS OR DAMAGE OF ANY KIND INCURRED AS A RESULT OF THE USE OF THE SITE OR RELIANCE ON ANY INFORMATION PROVIDED ON THE SITE. YOUR USE OF THE SITE AND YOUR RELIANCE ON ANY INFORMATION ON THE SITE IS SOLELY AT YOUR OWN RISK.
Post time: Sep-08-2023